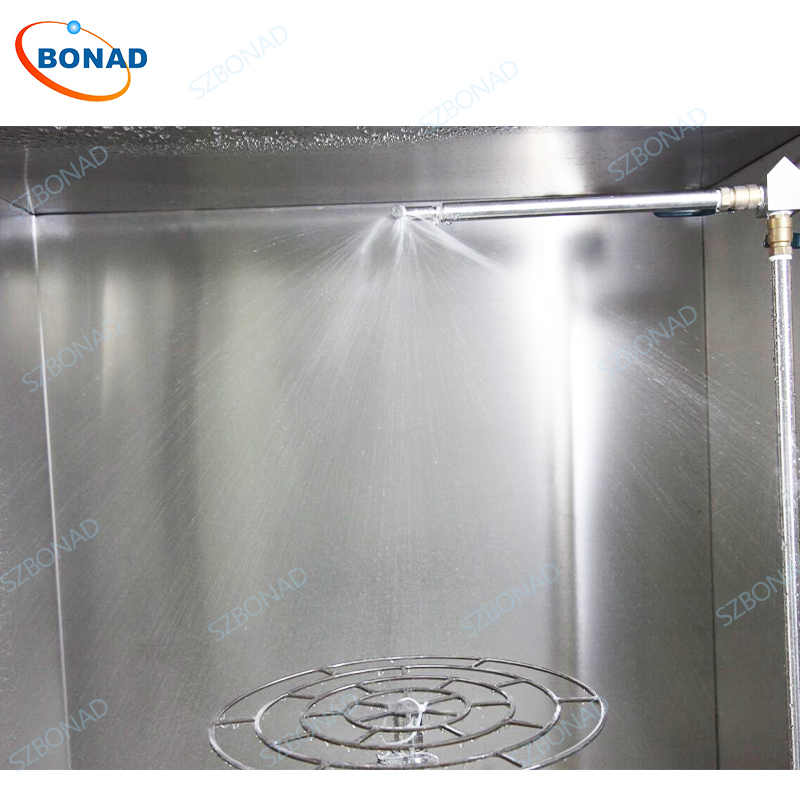
Understanding JIS D 0203 Testing: Comprehensive Guide to Moisture, Rain, Spray, and Dip Tests for Automotive Parts
JIS D 0203 Testing: A Comprehensive Guide
JIS D 0203 is a stringent ingress protection test standard established by the Japanese Standards Association. This standard is crucial for ensuring the moisture resistance and waterproof capabilities of various automotive parts. The scope of JIS D 0203 encompasses several specific tests designed to evaluate how well automotive components can withstand exposure to moisture, rain, spray, and immersion.
Testing Procedures for JIS D 0203
Automotive parts undergoing JIS D 0203 testing are subjected to a series of rigorous tests to ensure their durability and reliability in different environmental conditions. Here’s an overview of the primary testing methods:
Moisture Testing
1. M1 – Moisture Test: This test evaluates the performance of automotive parts when exposed to moisture over an extended period. The duration of this test is set at eight hours.
2. M2 – Moisture Test: This test focuses on assessing the functionality of parts under high temperature and humidity conditions. It lasts for one hour.
Rain Testing
Rain testing simulates real-world conditions where automotive parts are exposed to rainfall. There are two primary protocols under this category:
1. R1 – Rain Test: This test examines how parts function when subjected to rain droplets for a duration of 10 minutes at a water temperature of 32 degrees Celsius.
2. R2 – Rain Test: This protocol assesses the functionality of parts exposed to indirect wind and rain or spray for 10 minutes at a water temperature of 60 degrees Celsius.
Spray Testing
Spray testing involves using specific nozzles to direct water onto automotive parts from a certain distance and flow rate. Two main protocols are followed:
1. S1 – Spray Test: This test investigates how parts perform under direct wind and rain or spray conditions for 30 minutes with a minimum water flow rate of 24.5 liters per minute.
2. S2 – Spray Test: This test is more intense, subjecting parts to heavy water spray for one hour with a minimum flow rate of 39.2 liters per minute.
Dip Testing (Immersion Testing)
Dip testing, also known as immersion testing, evaluates how well automotive parts can withstand being submerged in water. There are three distinct dip tests within JIS D 0203:
1. D1 – Dip Test: This test assesses the functionality of parts that occasionally get immersed in water for five minutes, with submersion up to their upper surface.
2. D2 – Dip Test: This test determines the performance of parts that are continually submerged or designed to be completely waterproof for ten minutes, submerged up to 100 millimeters from their upper surface with a temperature difference of 30 degrees Celsius between the unit and the water.
3. D3 – Dip Test: This specialized test examines the waterproofness of parts used in unique applications by submerging them up to 100 meters from their upper surface for twenty minutes with a temperature difference of 50 degrees Celsius between the unit and the water.
Conclusion
JIS D 0203 testing is essential for ensuring that automotive parts can withstand various environmental challenges related to moisture, rain, spray, and immersion. By adhering to these rigorous standards, manufacturers can guarantee that their products meet high levels of durability and reliability.
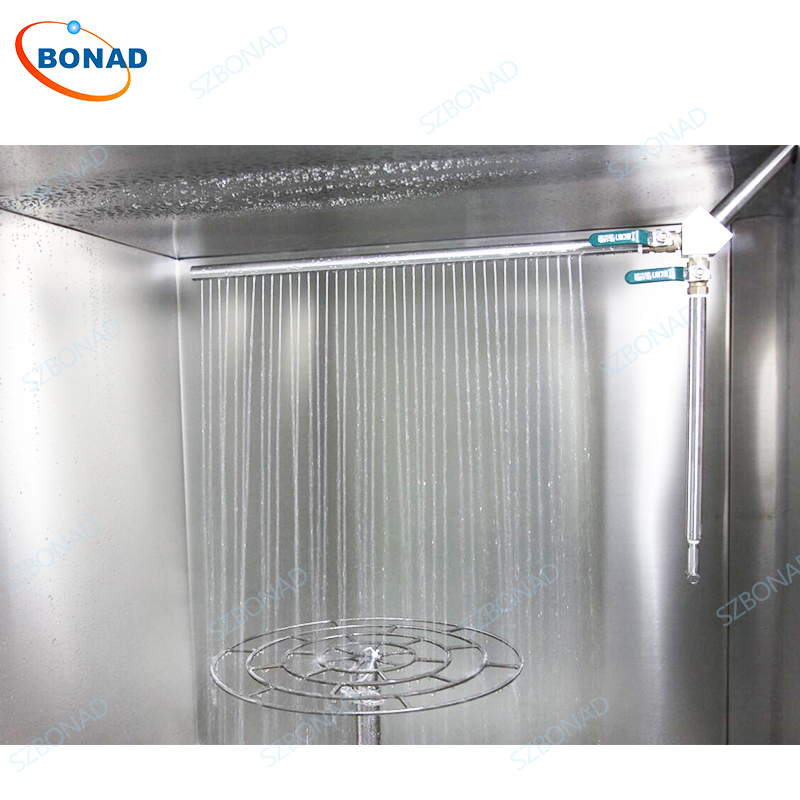
|